The track roller is used to support the weight of the tractor, while rolling on the track (rail link) or track shoe surface of the track, and it is also used to limit the track to prevent lateral slippage. The track roller force the track to slip on the ground when the tractor turns.
The track roller are often in mud, water and dust and are subject to strong impacts, so they are required to have reliable sealing and wear-resistant rims.
Features and Requirements
The function of the track roller is to transmit the weight of the locomotive group to the ground and roll on the track. In order to prevent derailment, the track roller should also be able to prevent the track from moving relative to it laterally.
The track roller often work in muddy water, sand and sand, and bear strong impact. The working conditions are extremely bad, and the rim is easy to wear.
The requirements for the roller are: wear-resistant rim, reliable bearing seal, low rolling resistance, etc.
prone to problems
(1) The wheel body is worn. The reason for this is that the steel used is unqualified or the hardness of the material during heat treatment is low and the wear resistance is insufficient;
(2) Oil leakage. The roller shaft is constantly rotating through the shaft sleeve, and the wheel body needs to be lubricated with oil, but if the sealing ring is not good, track roller it is easy to cause oil leakage, so the shaft and the shaft sleeve are easy to wear without lubrication. cause the product to be unusable. The reasons for oil leakage are as follows: 1. Unqualified floating oil seal; 2. Insufficient roundness of product shaft sleeve; 3. Insufficient gloss of fulcrum; 4. Substandard gear oil; All of the above problems will cause the oil leakage of the track roller.
Oil leak inspection and exclusion
- During the installation process, it should be strictly inspected according to the technical requirements of the parts, keep it clean, and prevent impurities from entering the installation surface. Especially on the sealing end face of the sealing ring, even tiny dust particles will damage the sealing and cause oil leakage.
- The sealing sleeve and the sealing rubber ring need to be replaced with new ones if they are aging, deformed, scarred or broken.
- The spring should be replaced when its elastic force is insufficient, and the uneven end surface can be ground. When the pressure ring is warped, it should be repaired and leveled, and sharp edges should be removed.
- The large and small sealing rings are not in strict contact and can be re-ground to make them have a uniform and continuous grinding ring. Do not hit the ring end face and disturb the mate ring. The thickness of the ring should be the same, otherwise it must be replaced.
- The thickness of the rubber ring is not enough, it is allowed to wrap the asbestos rope to make it reach a tightness of 0.15~0.20 kg per square centimeter.
- The wheel axle is bent, out of circle or the neck is worn, the wheel hub of the roller and the wear of the matching belt of the sealing shell must be repaired.
- When the plane of the bearing and the sealing ring is worn, a 2-4 mm thick oil-resistant rubber ring can be placed between the sealing sleeve and the end face of the hub according to the degree of wear. When installed, the gland assembly should rotate freely on the hub. In addition, a washer with an outer diameter of 100 mm, an inner diameter of 85 mm, and a thickness of 1.5 mm can be placed between the outer ring of the bearing and the support shoulder of the seal housing to compensate for the amount of bearing wear. When the height of the sealing sleeve is less than 32 mm and the width of the bearing is less than 41 mm, it should be replaced with new products.
- The paper pad on the roller should be kept intact and of suitable thickness
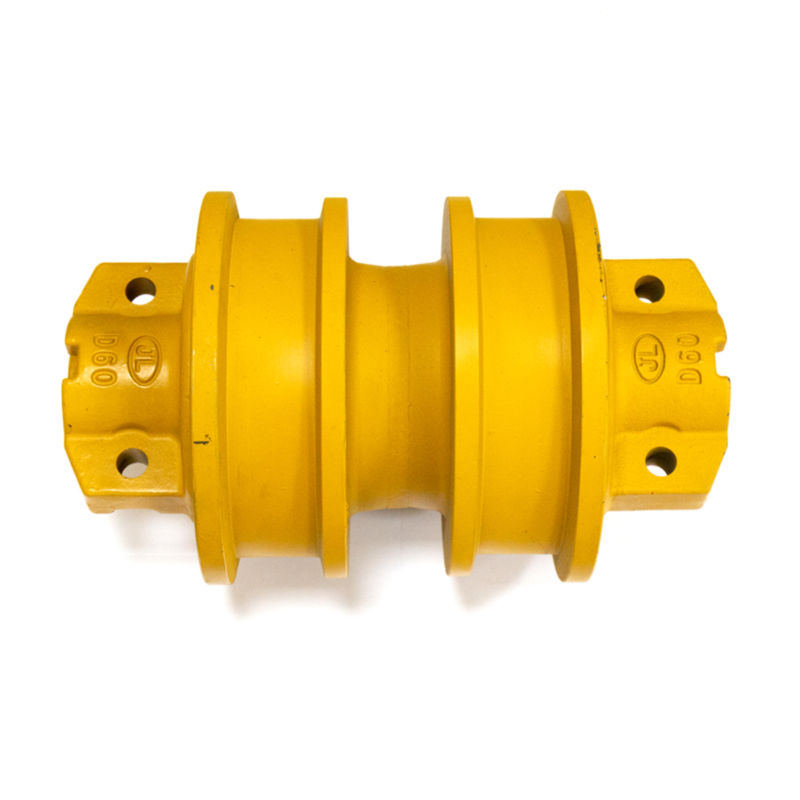